| Step
31. This picture makes my eyes go funny. We had a bad spell of weather and
the low light level made a blurred picture. This
is a dummy frame to fit to 3.5" hard drives to make them look like and fit
like the older 5.25" drives. | |
|
|
Step
32. Here is the drive fitting snugly into the frame and connected to power
and data. |
|
|
|
Step
33. The drive tray complete.
We had previously formatted and installed software onto the hard dirve using
software we have on the Macintosh that enables us to build Synclavier software
and install sounds. 1000's of lovely FM patches and 100's of samples ready to
be converted into new previously unimagined FM sounds with Resynthesis.
|
|
|
| |
| Step
34
For the first time in its new short life the Sync II powers up and boots
under its own steam. The three red lights that glow on the HOP box means that
we achieved a successful boot. |
|
Step
35. And here is the proof, the Synclavier Release 0 welcome screen.
We are using the Mac purely as a dumb terminal, all processing and screen plotting
is performed by the Synclavier's internal ABLE processor. | |
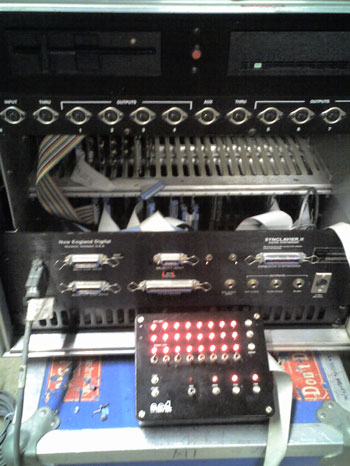 |
| Step
36. Now we fit enough MIDI ports to run an entire neighbourhood. Shown
here undergoing test, the lights on the HOP box flahing so rapidly that they appear
to be all on. |
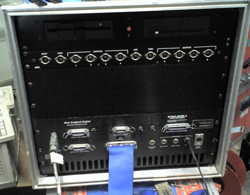
|
Step
37. This is an invisible step. The observant among you may have noticed
that the front panel has been fitted in the photos of this page. We had rewired
and fitted connectors where needed to the front panel. Because we upgraded the
processor, support cards, and drives the cabling was no longer correct and no
longer any use to us so had to be replaced. This was too boring to take a picture
of and took a good deal of time with very little visual impact. (OK, we forgot
to take before and after pictures0 Here is the
finished case after audio test has been completed. | |
|
|
| Step
38. Now for the keyboard. Our final stage. Here you see the front panels removed
to enable us to clean and lubricate the buttons. Sweat is our biggest problem,
after years of use it gets into the buttons and makes then 'sticky' in operation.
Since these are military buttons out of the B52 bomber they will be like new after
a bit of spit and polish.
. Each
panel is cleaned of dust, dirt, drink, sweat and treated to preserve the fascia.
Then Each panel is carefully lined up with the buttons to ensure they are not
fouling the openings. |
|
Step
39. Removal and cleaning of keys. Under the keys dust and dirt accumulates
which can only be accessed by removing every key.
Each key is unique and can
only fit in its own position. We take this opportunity to clean every key (they
are wooden with a laqueured acrylic coating). The laqueur needs sweat and grime
cleaned from it. We have a special cleaning solution that removes sweat and polishes
the surface with no abrasion or damage and leaves no residue such as silicon which
would feel bad and attract dust.It's a long laborious task but worth it when you
see the keys gleaming like new again. |
|
|
|
|
| Step
40.
The keyboard in the process of being reassembled. When every key
is fitted then we test and calibrate every keys response to pressure and velocity.
Every keyboard is unique to each machine and has its own data table of calibration
which the computer refers to.
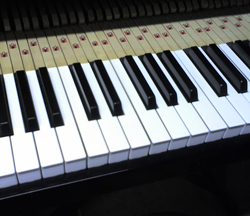
And
finally the keyboard with gleaming teeth after a trip to the dentist. |
|
| Step
41. The final stage. The complete assembled machine. (We
will do a pretty, staged picture tomorrow. The machine deserves it) Ready
for collection. |
|
|
| | |
|
| |